From the gently sloping shingles of a cozy cottage to the dramatic pitched copper roofs of European cathedrals, the roof is an essential part of a home. It offers protection, contributes to a building’s energy efficiency, and serves as an expression of architectural style.
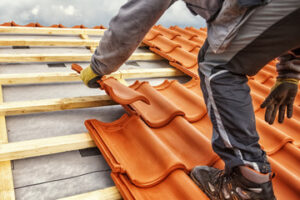
A key component of the roof is sheathing, or decking. This is typically made from plywood or oriented strand board. Visit https://www.bostonroofingco.com/ to learn more.
The roof is a significant part of any home’s structural integrity and offers protection against the elements. It is therefore essential that it be made from the right materials to ensure durability and longevity. There are many different types of roofing materials to choose from, each with its own advantages and life lengths. Choosing the appropriate material will depend on a number of factors, including budget and aesthetic preference.
Asphalt shingles are a popular choice for new roofs due to their cost-effectiveness and range of color options. However, they do not offer much fire resistance and are less durable than other roofing materials. Slate roofs are a more luxurious option, and can last up to 100 years with regular maintenance. However, they are also more expensive and can be difficult to install on historical homes.
Metal roofs are another durable roofing option, and can last up to 50 years. They are available in a variety of finishes, such as aluminum, zinc, and copper. They are also a good choice for historic homes, as they can match the appearance of early shingles. However, some historical societies discourage the use of substitutes for original shingle materials, so it is important to check with them before making a decision.
A common flat roof material is EPDM membrane, which comes in large sheets that minimize the need for seams. It is then mechanically fastened to cover boards or insulation and sealed with a hot-air gun. This type of roof can be used in commercial buildings or on homes, and lasts 10-15 years.
Clay tile roofing was used extensively in colonial America and the 19th century, especially in areas of Spanish influence. It is also seen in revivalist styles such as Italianate and Richardson Romanesque, which favored rounded tiles.
Wood shingles were the most common roofing material from the earliest colonial days through to the 19th century. The quality, manufacturing techniques, and installation methods varied during this time. Some shingles looked similar to modern 3-tab shingles, and some resembled slate.
Decking
The roof deck is the essential layer of material positioned between the structural components of your home’s framing, such as trusses and rafters, and the outer roofing materials, including shingles or tiles. This critical component helps distribute the weight of the roof covering evenly and protects the inner layers from weather elements. Hence, it’s important to choose the right type of decking.
There are several different types of decking available, including plywood, oriented strand board (OSB), and wood plank sheathing. Each offers its own unique advantages. For example, OSB is engineered from overlapping wood strands and compressed for strength. This makes it less expensive than plywood and also resistant to moisture and rot. Meanwhile, plywood is made from many thin layers of cross-grained wood, which increases its durability, reduces splitting during nailing or cutting, and prevents warping over time.
When choosing your roof decking, consider the climate in your area and your budget. If you live in a region with high rainfall or humid conditions, moisture-resistant materials like OSB are a good choice. If you want a more traditional look, wood plank sheathing is an option that can provide a rustic or natural aesthetic.
Lastly, it’s important to choose a material that is durable and can withstand the load of your roof. If your home is located in an area with high winds, it’s recommended to use strong, thick, and long boards. If you choose to install a wood decking, make sure to use pressure-treated lumber or rot-resistant preservatives.
Once the decking is in place, it’s time to install the shingles or tiles of your choice. To ensure that the shingle or tile edges are properly secured, it’s a good idea to use a sealant. You should also use corrosion-resistant fasteners, especially when building in coastal areas.
In addition to the material used for your roof decking, other factors that determine the quality and cost of your roof include footings, trusses or rafters, and insulation. It’s also important to evaluate your home’s foundation and drainage system, as this will affect the longevity of your roof.
Collar beams
Collar beams are a common element in domestic roof construction. They are sometimes referred to as collar ties, but this is inaccurate. A tie in building construction works in tension rather than compression, and most collar ties are designed to keep rafters from sagging and not to connect ceiling joists.
Home inspectors should be familiar with the differences between these structural members, as they serve different purposes and have distinct requirements. A collar tie or rafter tie is a horizontal member that runs between two rafters. It is used to prevent rafters from detaching from the ridge, and it helps to distribute the load of the roof evenly. A ridge strap is another option for resisting uplift forces from wind.
Both a collar tie and a ridge strap are essential components of a roof frame, but they differ in terms of their purpose and requirements. A collar tie is a horizontal structural member that connects the rafters in a triangular roof truss. It is often found in houses with steeper slopes, and it helps to distribute the load of a roof evenly. It is also a good way to reduce the risk of sagging.
In addition to their function, collar ties can contribute to the aesthetics of a home’s interior or exterior. They can be crafted in a variety of styles and materials, from simple for a minimalist look to intricate and decorative for more ornate designs. Alternatively, they can be left exposed to create a rustic look.
When constructing a collar beam, it is important to ensure that it is properly sized and spaced. A poorly sized collar tie can lead to a number of problems, including sagging and loosening of the roof. This is why it is essential to consult a professional engineer before constructing a collar beam.
Some builders have questioned the need for collar ties, but they are essential for roof frames. They are particularly useful in high-pitched roofs where sagging is more likely to occur. Collar ties help to distribute the roof’s weight more evenly, which can reduce the risk of sagging. They can also minimize the deflection of undersized rafters by transferring some of the load to rafters on the other side.
Re-roofing
The roof of a home is one of the most important investments any homeowner can make. It protects the interior of the house and increases the property value. Therefore, it’s important to take care of any damage to the roof as soon as possible. A new roof can last for years and keep the structure of a building protected from weather elements. It is also an attractive feature that can add curb appeal to a home. However, determining whether the roof needs repair or replacement can be tricky. Many homeowners are unsure if the damage is severe enough to require a full roof replacement, or if a reroofing would be sufficient.
Re-roofing is a process of laying down an additional layer of shingles on an existing roof without tearing it off. It is often used on shingle roofs that are damaged or worn, but it’s not suitable for metal roofs and flat EPDM or PVC roofs. It’s not as durable as a full replacement, but it’s an affordable option for those who want to extend the life of their roof.
During the re-roofing process, special drip-edge flashings are installed at the eave and rake to prevent water leakage. The flashing can be made of metal, plastic or wood. In most cases, it is nailed down to the sheathing with nails driven at high points. Some roofers also install a layer of waterproof shingle underlayment (WSU) over the drip edge for added protection from moisture and sun damage.
A re-roofing job requires a lot of work and preparation. First, the old shingles are removed. Then, the succeeding courses of shingles are laid over the old shingles. At the ridge, the shingles are cut so that they butt closely together and do not overlap. The shingles are then secured with the help of a starter course. Finally, a ridge cap is placed at the end of each shingle row to protect it from moisture.
Recovering a roof is a time-consuming and expensive project, but it is an effective way to extend the lifespan of a roofing system. However, it’s important to consider the cost of a complete roof replacement before deciding on this solution. A full roof replacement will allow you to inspect the underlying layers of your roofing system, and will resolve any structural problems that may be hidden under the shingles.